پالایشگاه ها،نیروگاه ها،کارخانه ها،معادن و تمام تأسیسات صنعتی دیگری که میشناسید در کنار تمام مزایا و تمام محصولاتی که برای هر یک از ما انسان ها به همراه دارند همواره دارای خطرات قابل توجهی بوده و هستند.خطراتی که در طول تاریخ باعث کشتن و مجروح شدن هزاران نفر شده است. [لیست فجایع صنعتی تاریخ بهمراه تعداد کشته های هریک] آیا به صفر رساندن این خطرات ممکن است؟چه راهکاری برای این مشکل وجود دارد؟آیا مفهوم SIS برای حل این مشکل طرح شده است؟
در ابتدا باید بدانید به صفر رساندن خطرات کار غیرممکنی است اما به حداقل رساندن آنها میسر است.از مهمترین تیم ها در هر پروژه ی صنعتی و تأسیساتی گروه مهندسین ایمنی (Safety Engineers) و مطالعاتی است که بر عهده ی آنها است. این مطالعات از اولین گام ها یعنی تخمین های نخستین برای ایجاد یک پروژه ی تأسیساتی شروع میشود و تا بررسی انجام صحیح و بدون خطر فرآیند،اقدامات برای کاهش ریسک در طول فرآیند،حدس خطرات پیش از بروز آنها و رفع خطرات پیش آمده ادامه دارد.
در این مقاله اختصاراً به کاهش ریسک های صنعتی توسط تیم های ایمنی ، فرآیند و کنترل در پلنت های صنعتی میپردازیم. و سپس کمی با اصطلاحات فنی این حوزه ارتباط برقرار میکنیم؛ پس با ما همراه باشید :
مطالعات امکان پذیری یا Feasibility Study :
برای بنا کردن یک پلنت،شرکت های بزرگ پیمانکار در ابتدا نیاز به برآوردکردن فاکتورهایی دارند. از جمله مهمترینِ این موارد میتوان به برآورد هزینه ی اولیه ی ساخت،بررسی میزان مفید بودن محصول نهایی و سود آوری آن در هر بازه ی زمانی،برآورد مساحت بنا و حتی بررسی محیطی که قرار است در آن ساخت و ساز انجام شود اشاره داشت.
برای مثال جهت تولید استیل نیاز همیشگی به آب وجود دارد . پس برای ساخت کارخانه ی استیل بهترین محیط محلی است که به آب های آزاد دسترسی بیشتری داشته باشیم. قطعاً ساخت آن در محیطی کویری از بازدهی های آن میکاهد . هربار آب رسانی به این محیط کویری چه مقدار زمان و هزینه ی اقتصادی به همراه دارد !؟
به این دست مطالعات اولیه که مبدأ ساخت پلنت های صنعتی است مطالعات امکان پذیری یا Feasibility Study میگوییم . همواره باید نقش این مطالعات را جدی گرفت. چرا که اگر ساختار اولیه ی یک بنا اشتباه چیده شود اصلاح آن بسیار سخت و حتی غیر ممکن خواهد بود . Feasibility Study در واقع مانند یک نقشه وظایف دپارتمان های مختلف مهندسی را در دید اولیه ترسیم میکند. و کل فرآیندهای پروژه را در یک نگاه می بیند . نهایتاً هم انتظار دارد فرآیندها منطبق بر آن پیش بروند و با بالاترین بازدهی به ثمر بنشینند .
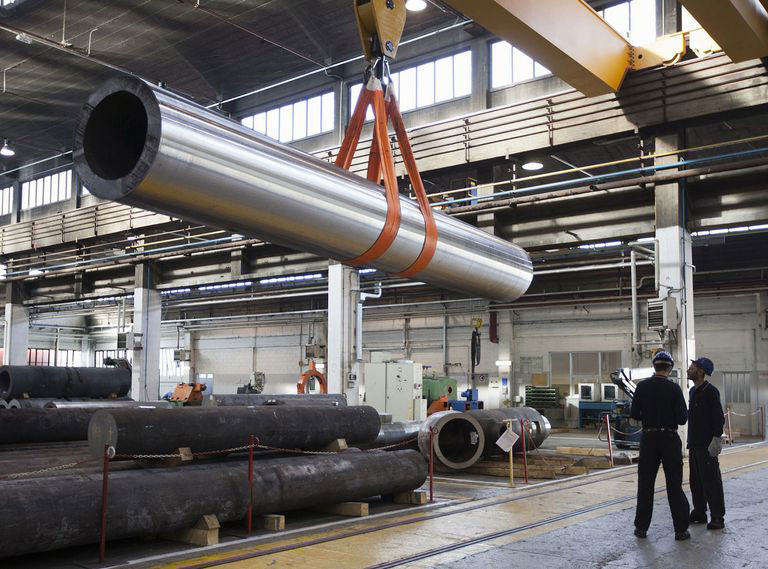
تصویر یک کارخانه ی تولید فولاد
لایه های ایمنی تأسیسات :
پس از ساخت پلنت باید به نکات ایمنی در طول فرآیند توجه داشت.اینجا شروع فعالیت اصلی مهندسین ایمنی و فرآیند است. یک پالایشگاه نفت خام را در نظر بگیرید.نفت خام از طریق خطوط وارد پالایشگاه میشود. و در واحدهای مختلف روی آن فرآیندهایی انجام میشود. تا نهایتاً در برج های تقطیر با دماهای بسیار بالا به مشتقات مختلف قابل استفاده از جمله بنزین تبدیل شود.
اولین لایه ی ایمنی در پلنت از همین جا یعنی مرحله ی طراحی و انجام فرآیند شروع میشود . اینکه فرآیندها با چه هدف و چه ترتیبی طی شوند توسط دپارتمان های ایمنی و فرآیند مهندسی میشود.در همین مرحله هم اگر اشتباهی رخ دهد باعث خطرات جانی و اقتصادی خواهد بود . بطور مثال میدانیم نفت خام عموماً حاوی مقدار زیادی H2S است و این ویژگی،خاصیت ترش بودن به سیال میدهد.خطرناکی H2S به حدی است که در دز های بسیار بالا حتی باعث تجزیه انسان هم میشود. و در دز های پایینتر انسان را با چند دم و بازدم میکشد.حال اگر در فرآیندها واحد شیرین سازی سیال در نظر گرفته نشود و در کوچکترین نقطه ای نشتی سیال داشته باشیم مهندسی اشتباه فرآیند میتواند جان چند نفر را به خطر بیاندازد؟
در همین راستا ایمنی در این مرحله به مهندسی دقیق فرآیند و انتخاب تجهیزات با دقت بالا میپردازد.اگر در طی فرآیند خورندگی داریم از بدنه های ضد خورنده استفاده شود،اگر محیط Hazardous Area است از تجهیزات ضدانفجار استفاده شود ، سایز تجهیزات از جمله ولوها،گیج ها،ترانسمیترها و … منطبق با نیاز پروژه باشد تا نشتی سیال نداشته باشیم و … .
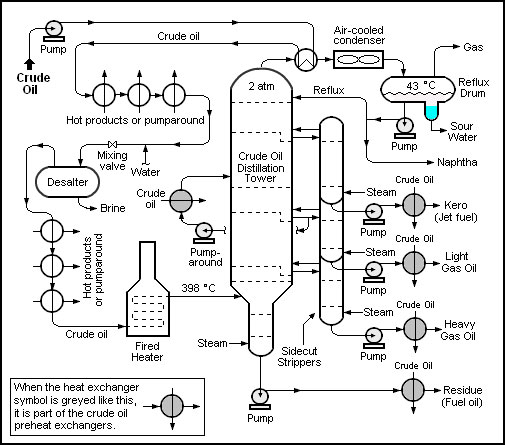
تصویر فرآیند تقطیر نفت خام
لایه های دوم و سوم ایمنی :
گام دوم ایمنی استفاده از سیستم های کنترل فرآیند (Basic Process Control System) است.در این مرحله توسط ساختارهای کنترلی پیاده شده روی پلنت،اپراتورهای متخصص از اتاق کنترل به عملکرد صحیح تجهیزاتی که در مرحله ی اول در سطح پلنت نصب شده اند نظارت دارند.بطور مثال اگر جریان سیال در خطوط کمتر یا بیشتر از حد انتظار باشد آنها قبل از بروز هرگونه مشکل بکمک سیگنال های کنترلی به اصلاح آن میپردازند تا از افت فشار یا بالارفتن بیش از حد فشار (Over Pressure) جلوگیری شود.
کنترلرها در اتاق کنترل همانند PLC ها ، سنسورها همانند ترانسمیتر فشار،ترانسمیتر سطح،ترانسمیتر دما و… ، عملگرهای کنترلی مانند کنترل ولو ها یا ولوهای On/Off از جمله تجهیزات اصلی سیستم های کنترل هستند.
مرحله ی سوم به آلارم ها یا اخطارها میپردازد.در لایه ی دوم اپراتورهای کنترلی با تدابیر پیش بینی کننده ی خود وظیفه ی نظارت و کنترل فرآیندها را در مواقع نیاز برعهده داشتند.مرحله ی سوم یک قدم بالاتر از آن و هنگامی است که آلارم های سیستم هشدارِ عدم کنترل بر فرآیند را میدهند و به اپراتورها این موضوع را میرسانند که آن قسمت خاص از پروسه نیازمند رسیدگی است.
تا به حال با سه لایه ی اصلی ایمنی آشنا شده اییم . طبق تعاریف و استانداردها نقش هر لایه آنقدر مهم و حیاتی است که به اندازه ی 10 برابر لایه ی ایمنی قبلی خود را تقویت می کند . اما علاوه بر این سه،آیا باز هم نیاز به استفاده از ایمنی های بیشتر در تأسیسات وجود دارد ؟
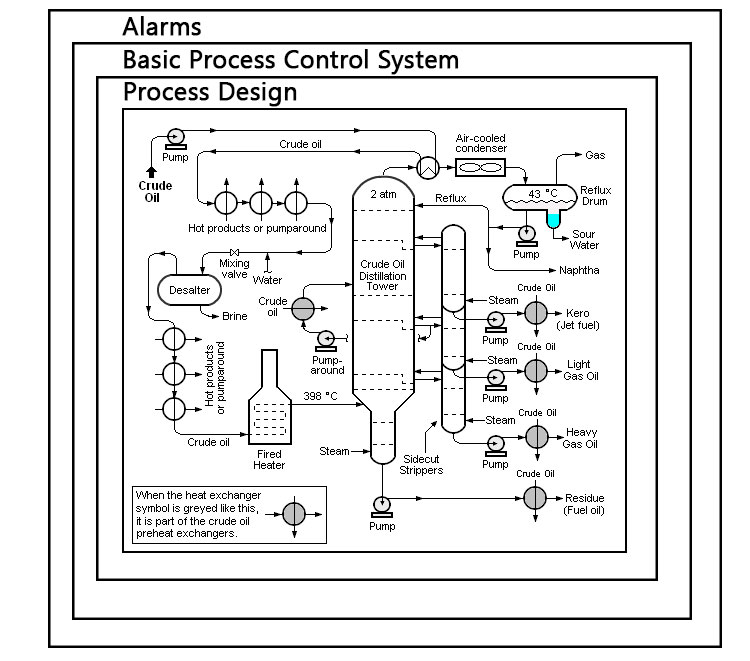
تصویر لایه های ایمنی تأسیسات
استانداردهای جهانی در این رابطه :
با تمام این تمهیدات،در طول تاریخ بازهم شاهد حوادث ناگوار و مرگ هزاران انسان بوده ایم. این اتفاقات،این اخطار را به مجامع بین المللی داد که هنوز نیاز به اجرای سیستم های دقیقتر برای بالابردن امنیت تأسیسات است.بنابراین مجامع مهندسی جهانی متشکل از مهندسین اروپایی،آمریکایی ایده ی ایجاد یک عملکرد جدید برای کنترل بیشتر روی کل فرآیندهای پلنت ها را دادند و استانداردهای ISA 84 و IEC61508 پیرو این موضوع تشکیل شدند.بعدها استاندارد آمریکایی ISA و استاندارد اروپایی IEC ادغام شدند و استانداردی یکپارچه و جامع تر تحت عنوان ISA84/IEC61511 را شکل دادند.اما راهکار،اضافه کردن یک سیستم کنترلی خاص در کنار سیستم کنترلی پایه ای به عنوان لایه ی چهارم امنیت بود.این لایه SIS یا Safety Instrumented System نام داشت.
نمودار لایه های ایمنی تأسیسات
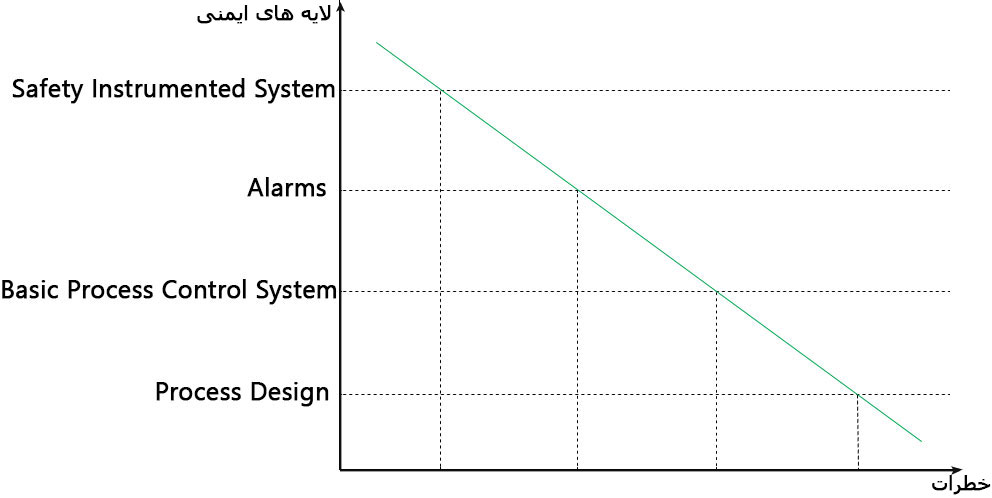
SIS یا Safety Instrumented System چیست ؟
همانطور که گفته شد SIS یک سیستم کنترلی مجزا در فرآیندها ، در کنار سیستم کنترلی اصلی است.تصویری که میبینید بخشی از فرآیند یک پلنت نیروگاهی را نشان میدهد.
سیال داخل تانک از طریق خطوط انتقال به راکتور منتقل میشود و بدین صورت فرآیند انجام میپذیرد.سیستم کنترلی اصلی در مقیاسی ساده شامل یک سنسور LT برای بررسی سطح سیالِ داخل راکتور،یک کنترلر مانند PLC برای ارسال فرمان کنترلی در مواقع نیاز و یک شیر کنترلی برای دریافت فرمان و تنظیم ورودی سیال به راکتور در مواقع عملیات است. اما در کنار این مجموعه،مجموعه ی کاملاً مجزای SIS شامل یک سنسور PT برای سنجش فشار سیال،یک کنترلر مانند PLC (که به آن Logic Solver هم میگویند) برای ارسال فرمان کنترلی و یک شیر برای اجرای فرمان ها است.سیستم کنترلی SIS سیستمی با حساسیت و دقت بسیار بالا است و بسته به شرایط و خواست ما از فرآیند میتواند از سنسورهای مدنظر در طراحی آن استفاده شود . حساسیت بالای SIS کمک میکند تا در شرایط خطر مانند یک سیستم قطع اضطراری عمل کند . SIS سیستمی Redundant است .
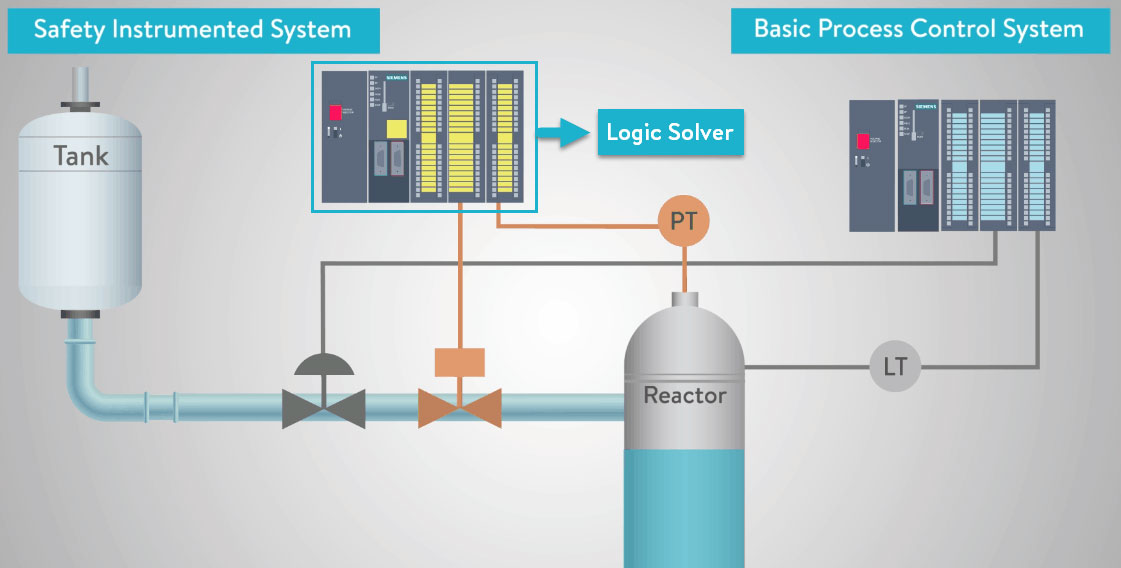
بخشی از فرآیند شامل SIS
سیستم های کنترلی جایگزین یا Redundant Control System :
سیستم کنترلی SIS یک Redundant Control System است . یعنی چه ؟ در ابتدا به مفهوم عبارت Redundant میپردازیم .
همانطور که متوجه شدیم SIS سیستم کنترلی جایگزین است و فقط در مواقع بسیار حساس و خطرناک وارد عمل میشود . به تجهیزات یا سیستم های جایگزینی که در کنار سیستم اصلی قرار میگیرند و در مواقع خاص جای سیستم اصلی را پر میکنند Redundant میگویند . همچنین این ساختار Redundancy نام دارد . Redundancy بطور قابل توجهی امنیت فرآیندها را بالا میبرد اما به همان نسبت هزینه ها را چند برابر میکند . چرا که در نظر داشته باشید در همین مثال،SIS علاوه بر سه جزء اصلی ، سه جزء دیگر داشت. شامل یک کنترلر،یک سنسور و یک ولو اضافه.این استراتژی هزینه ها را برای این قسمت بسیار کوچک فرآیند حداقل دو برابر کرده است. اما گاهی باید هزینه ها را فدای امنیت بالاتر بکنیم .
در بخش دوم این مقاله با مباحث تکمیلی مطالعات خطر و ایمنی میپردازیم و با مفاهیمی همچون SIL و HAZOP بحث را ادامه خواهیم داد.پس با ما همراه باشید .